The New Lean and Green Economy – Learning to Do More with Less!
The New Lean and Green Economy is bringing businesses, government, and communities together to engage in advancing a new integrated economic and ecological model that cannot be sustained for future generations without a new way of thinking and working.
This new model will transform the way we do manufacturing; produce and consume energy; manage the land; grow the food we eat, and the way we work and live. Automation, artificial intelligence, global competition and an evolving workplace are all factors changing the way organizations are becoming more sustainable in the New Economy. Sustainability Sustainability is a relatively new term that describes how to make sure the human economic systems last longer and have less impact on the natural ecological systems. It particularly relates to the concern over major global problems relating to the depletion of natural resources and increased carbon emissions. Sustainable focuses on the elimination of waste by minimizing the consumption of resources (human and natural capital) to effectively maximize the creation of value for its customers, stakeholders, and communities. Human Capital pertains to business practices relating to labor and the community/region in which a corporation conducts its business. Natural Capital refers to sustainable environmental practices to benefit the natural order as much as possible or at the least, do no harm and curtail the environmental impact.Lean & Green Concepts
Lean & Green (L&G) concepts are complementary and to some degree overlapping. Both concepts require changed mindsets and establishment of cultures supporting the philosophy underlying each concept. Hence, the analysis shows that these concepts display similarities at the level of resource productivity, organizational change, and resource reduction as show below:
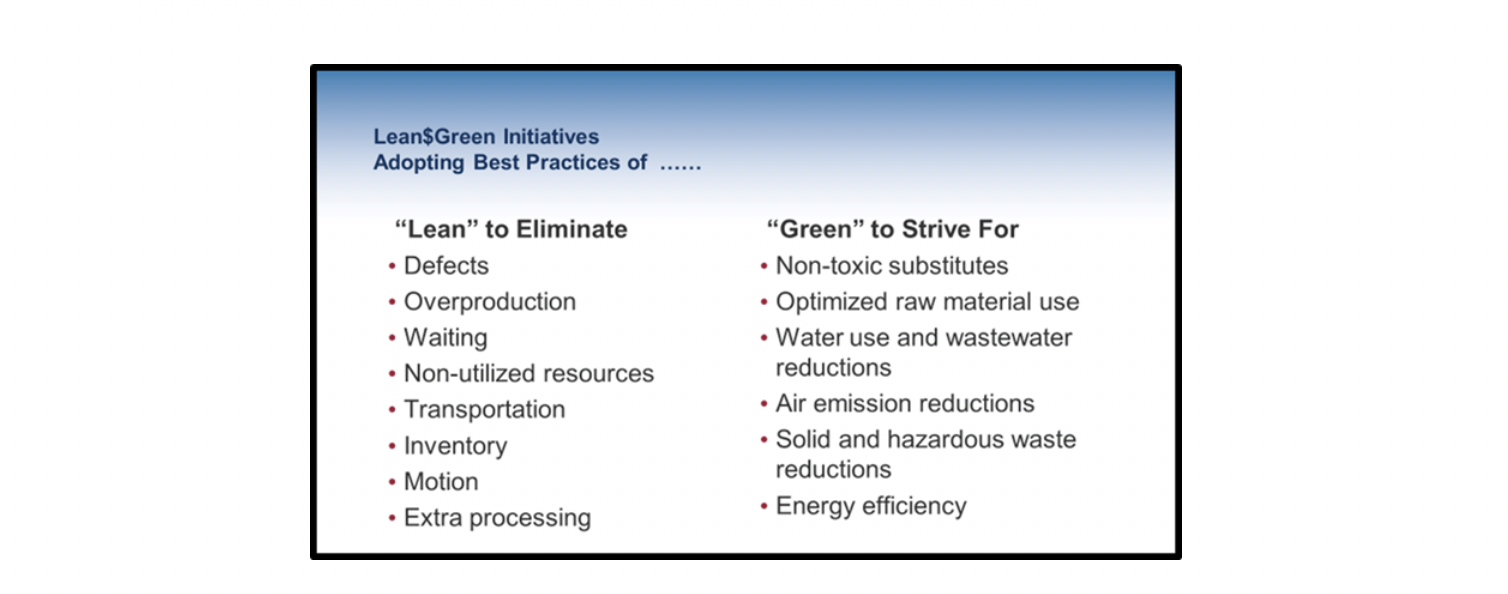
Today, many U.S. manufacturers are reevaluating their production and sourcing locations and are taking a closer look at the benefits of reshoring. The Reshoring Initiative promotes and enables the practice of bringing manufacturing and services back home from overseas. Reshoring benefits manufacturing companies by reducing the total cost of their products, improving balance sheets, and making product innovations more effective in reducing the wastes related to human and natural capital.
Leverage Learning Networks
Lean & Green advocate are coming together to formulate and share the next generation of values, principles, initiatives, and jobs. Michael Porter, Bishop William Lawrence University Professor at the Harvard Business School explains, “The enduring competitive advantage in the global economy lies increasingly in local things – knowledge, relationships, and motivation – that distant rivals cannot match.”
An example of this type of collaboration already exists in North America where companies are engaged in organization-to-organization exchange for performance improvement. The MIT Sloan Management Review refers to these consortia as “Leveraged Learning Networks”.
No one organization has all the answers to deal with the economic and ecological challenges in this new Era of Sustainability. The Association for Manufacturing Excellence (AME) is joining with other learning organizations and businesses in supporting a close economic, social and cultural relationship.
To facilitate that transformation AME has established Consortia, a group of local companies (20 +/-) that collaborate for broad, deep, accelerated lean and green progress better, faster, and easier than they can do it alone. These dynamic practitioner-to-practitioner networks are designed to support and accelerating their journey toward excellence.
Next Generation of Lean and Green Thinkers
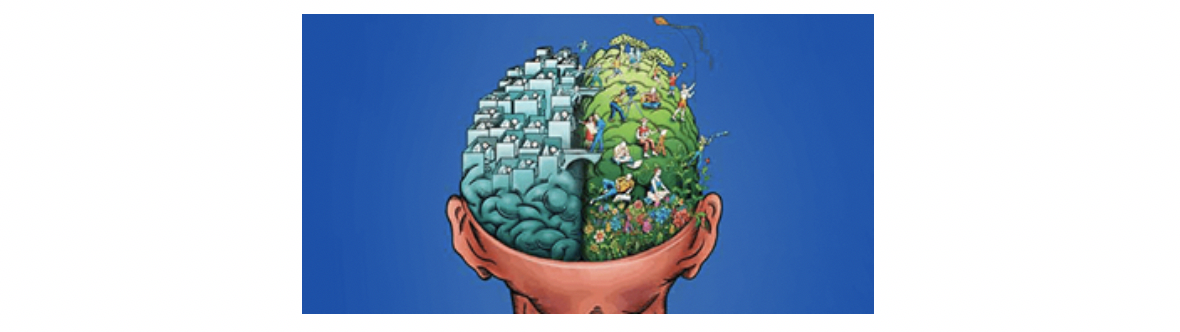