Taking Matter into his Own Hands
Printed below is a thoughtful investigation of the skilled workforce gap as it relates to reshoring and U.S. manufacturing, by University of Akron student Sean Osborne.
For those of us working in any sector of manufacturing and even those who are not, the below average state of manufacturing in America has affected us in some way. People in our communities have lost jobs due to manufacturing’s downfall. Business owners have lost their life’s work due to offshore outsourcing. Blue-collar work has developed a name that is not sufficient for a person when seeking out a career path. We have lost sight of how to educate new workers and introduce them into the skilled manufacturing jobs America has retained. This has left us with a skills gap. These issues hit home for Harry Moser, and as the founder of the Reshoring Initiative, he took it into his own hands to help bring American manufacturing back to life.
The Reshoring Initiative is a non-profit company that is highly determined to bring these jobs back to American soil by using Total Cost of Ownership analysis that shows companies the true cost of offshoring. Additionally, they do so by organizing community efforts to reintroduce manufacturing and skills training as a good career choice (Engineers, tool makers, welders, etc.). Moser’s family’s bond with manufacturing began over 100 years ago at Singer Sewing Machine in Elizabeth, NJ. At Singer, Moser’s grandfather was a foreman and his father managed nearly one third of the factory that, at the time, was the largest building in the world. Moser met with his decision to start the Reshoring Initiative when he drove past the factory and witnessed what his family, the city, and the country had lost to offshore production (Moser). “The Reshoring Initiative, founded in early 2010, takes action by helping manufacturers realize that local production, in some cases, reduces their total cost of ownership (TCO) of purchased parts and tooling. The Initiative also trains suppliers how to effectively meet the needs of their local customers, giving the suppliers the tools to sell against lower priced offshore competitors” (Engineers). After learning about Moser’s family history, I asked him if he could tell me how else he has seen offshore outsourcing affect manufacturing in America. His response was that he has seen dozens of American companies destroyed that were world leaders in industries like machine tools, foundry equipment, and shoe/textile machinery. He said that some of the devastation was because of offshoring delegated by United States corporate leaders. However, many companies just cannot compete with Japanese and German competitors because of a high United States Dollar, poor skilled workforce training, high corporate tax rates, and a lack of a Value Added Tax. On the other hand, Moser says many of these companies can still benefit from moving production back to America, especially if their main customer base is in America (Moser).
I was happy to learn more detail about how we have lost so many jobs and how the Initiative has been returning them. I was also curious to see if Moser had a view that was more open than the average person who seems to always be focused on one biased direction. Was he knowledgeable in concepts of what we would do if the offshored jobs began returning more rapidly? So I asked him, how can reshoring be possible in areas like machining with a lack of skilled workers? When I speak of the lack of workers, I am speaking of the skills gap and the talk of how most of the skilled working employees are at or near retirement age. Also, what can we do about the bad image manufacturing and blue-collar work has been given by society? His answer was the following:
The [first] challenge is to improve recruitment of more and smarter students into apprenticeship and community college programs. When we change the image of these skilled jobs and there are students demanding training, the problem will be fixed. To fix the image problem, see our Skilled Workforce program. Good news: the # of credentials awarded each year is rising rapidly. The [other] challenge is that society, including especially educators, is convinced that university degrees are the only path to success. This belief is despite the fact that about 40% of all workers with university degrees are in jobs that do not require such degrees. One key is to differentiate between statistical correlation of income with degrees vs. cause and effect. The smartest kids with the best connections go to university. Surprise: they make more money. Many would have made similar incomes in tool making or other skills fields (Moser 2016). His answer amazed me. I myself have worked in manufacturing for about eight years, and I know that the false image deters people that may have excelled in a career in manufacturing otherwise. There are a number of people forced to work in jobs outside of their expertise. People, like myself, could find their way to a career that makes them happy if only manufacturing was portrayed properly. Again digging deeper, I asked Moser to provide me with some pros to a career in a skilled trade, as opposed to a white-collar career such as being a lawyer. Once again his response was too good not to quote. These are what Moser believes to be the pros of a manufacturing career: “Deal with real objects, pride in work, computer technology, building instead of often tearing down, creating real value instead of transferring value, learn mechanical skills that help in the rest of life, be more self-reliant, be in demand instead of in excess, be part of the solution to a stronger U.S” (Moser 2016). All of these traits are desirable for people considering possible career decisions. Since Moser introduced me to the Skilled Workforce Program the Reshoring Initiative offers, I decided to investigate further. The Reshoring Initiative states that reshoring and manufacturing growth is possible only with a strong skilled workforce to back it up. The Skilled Workforce Development Program was designed to change some of the misperceptions about manufacturing and help communities motivate a higher quantity of quality recruits. This is done by informing people of the realities of a present day manufacturing career. For example, the importance of training, the revitalization of manufacturing, and opportunities for prestigious and financially rewarding careers. The three most common misconceptions people have had are that training is not as important as degrees, that manufacturing in the U.S. continues to decline, and that manufacturing jobs offer low prestige and income. The program requires community and political commitment but aides them in taking action on the matter. The key realities portrayed are that the importance of trade based training has not been properly promoted. Second, the success of reshoring and the attractiveness of a manufacturing career needs to be promoted. Last, our communities and politicians need to emphasize how the skilled people that work in the area they trained in, normally earn an income that is at the least comparable to university graduates (Engineers). I applaud The Reshoring Initiative for looking at the bigger picture and taking action beyond their original goal of simply bringing jobs back to America. Moser has committed his life and taken the risk of leaving his previous career at GF AgieCharmilles as president for 25 years and then chairman emeritus (Engineers). He did so in effort to lead America in efforts to bring back manufacturing jobs that have been lost to other countries and to keep the existing jobs from leaving. He has demonstrated that his goal is increasingly successful and can continue to work in our favor. Furthermore, Moser has outlined and offered guidance in filling in the rest of the gaps that need to be filled in order to successfully produce and retain the work as it returns. Throughout, my interview with Moser and my research on his Reshoring Initiative I quickly realized that he plays a very important role in returning America to the manufacturing powerhouse that it once was. Works Cited
Engineers, Dgs Marketing. "Home | Reshoring Initiative." Home | Reshoring Initiative. N.p., n.d. http://www.reshorenow.org/. Accessed 05 Oct. 2016.
Moser, Harry. Personal Interview. 2 Oct. 2016.
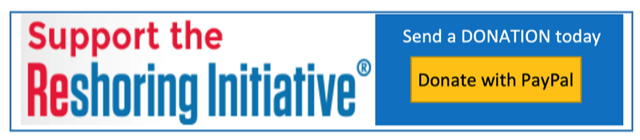